
If the bottle is filled immediately after blowing, such a bottle can be filled with 95℃ hot liquid īottles stored for more than 24 hours after blowing can only be filled with hot liquid at 88☌
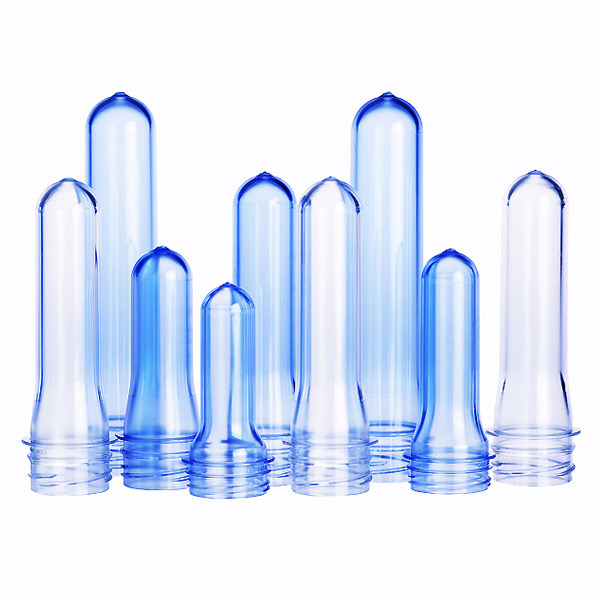
I.e., filling right after blowing, with a bottle storage period of fewer than 6 hours. However, many manufacturers have begun to use lightweight bottles and connected production in recent years. In general, the recommended placement time for hot fill bottles between the production of the preform and the filling of the beverage is:īottle storage period: >1L use within two weeks, <1L use within three weeks The higher the moisture content, the lower the heat-resistant temperature of the bottle. It will have an impact on the heat-resistant temperature of hot fill bottles. PET’s performance is directly influenced by its moisture content. It will absorb more water the longer it is left in place. It transports it to the bottle conveying line.īecause PET absorbs moisture, placing PET in the air (including slices, preforms, and bottles) will absorb moisture in the air. (7) When the bottle blowing process of blow moulder is finished, the bottle conveying manipulator removes the bottle from the mould. If there isn’t any air blowing out of the bottom mould, the bottom of the bottle will protrude, and the bottle will not be removed. High-pressure cooling gas is blown out of the hollow stretch rod at the same time to cool and shape the bottle wall.īlowing low-pressure air from the bottom mould for demolding is a good idea. (6) The exhaust begins after the high-pressure blowing is completed. On the other hand, to improve the crystallinity of the bottle body plastic, make the bottle wall close to the mould wall. (5) On the one hand, the high-pressure gas is kept in the mould for a specific amount of time, relieving internal stress caused by the stretching of the preform. When the stretching rod reaches the mould’s bottom, high-pressure air enters the cavity, stretching the preform even more and bringing the bottle wall closer to the mould wall. (4) Pre-blowing occurs after entering the blowing mould, stretching the preform in a ring direction.
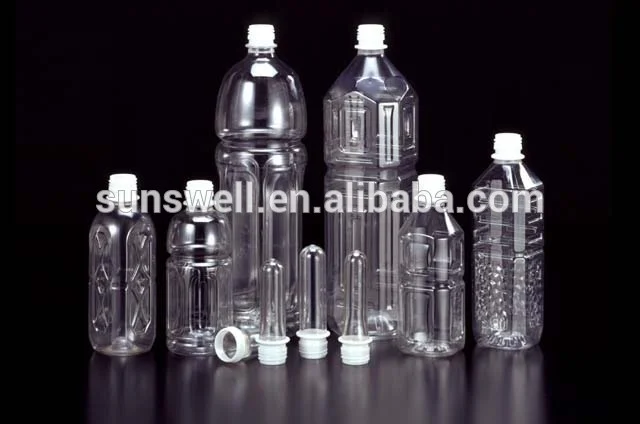
(3) The blank conveying manipulator feeds the heated preform into the bottle blowing station. The preform is then blown by the furnace fan to ensure that the inner and outer walls of the preform are evenly heated. (2) The preform heating furnace cools the bottle mouth as it rotates to ensure evenly heated while heating the preform. (1) The preform supply system sorts the preforms before transporting them to the preform heating furnace.
